Split chiller with a separately
installed condenser (liquefier)
Split chiller with a separately
installed condenser (liquefier)
WRK-S are L&R split chillers with a separately installed condenser. The heat from the refrigerating circuit is dissipated in the external condenser. The chiller is installed indoors. We produce these systems with cooling capacities ranging from 10 to 1,400 kW, which can be expanded by modules.
Chillers are fitted with piston or screw compressors, depending on the cooling capacity. Depending on the customer’s wishes, chillers are built with one refrigerating circuit or with a number of separate refrigerating circuits for greater operating security. The system is constructed according to the customer’s requirements. The system is constructed according to the customer’s requirements.
Do you need advice or do you have a question? Just send us an
Numerous options
for L&R split chillers
HEAT EXCHANGER
The demand-oriented design for a system concept is also an important point for heat exchangers, especially since transmission losses occur here that must be kept low. What transmission area is available? What is the heat transfer loss between the plates? Heat exchangers are required in order to separate the system, e.g. to prevent impurities or hazardous substances from entering the system.
WATER TREATMENT
Depending on the water quality and operating conditions, the use of special water additives is necessary to prevent deposits, corrosion and contamination. Corrosion inhibitors are added to keep corrosion rates low. The range on offer takes into account the materials, water quality and operating conditions. Combination products with a cleaning effect are often used to keep surfaces clean at the same time. Hardness stabilisers and dispersants can prevent new deposits and remove existing ones. In this case, having the appropriate filter technology is a prerequisite. The correct dosage is provided by quantity-controlled dosing pumps, depending on the level of water consumption. The use of broad-spectrum biocides is necessary to prevent system germination. Germs can attack materials, clog heat exchangers with slime and change the water quality. Regular doses prevent this.
VariKon
Conventional chillers operate at a fixed condensing temperature, which is usually around 47 °C. However, this temperature level is only required at high outside temperatures of approx. 35 °C. In cooler climates, a lower condensing temperature is totally sufficient: At an outdoor temperature of 8 °C, for example, the chiller is operated with a condensing temperature of 20 °C. For this reason, the VariKon controller regulates the condensing temperature on a sliding scale depending on the outside temperature, and can thus achieve significantly lower power consumption of the compressor.
EC Fans
Nowadays, highly efficient EC motors on the fans around the condenser should be speed-controlled, which means they are controlled according to demand and represent part of the energy efficiency of an overall system.
EXPLOSION PROOF
L&R has comprehensive experience in planning refrigeration systems for areas at risk of explosion, in accordance with ATEX Directive 94/9/EC. In systems that conform with ATEX standards, which L&R plans for chemical and process technology companies in particular, only appropriately certified electrical components are used. Static charges, sparks and increased temperatures can be reliably excluded, both while operating the system and in potential fault situations.
MHP – HYDROPHYSICAL WATER TREATMENT
Protects the system against impurities and blockages in the heat exchanger channels.
Reduces deposits of biological matter.
Stainless steel strainer basket filters with bypass for cleaning during operation.
PUMP-TANK SYSTEM
Avoid harmful, short compressor running times in chillers by using a sufficiently large tank.
Partition walls serve to avoid mixing temperatures.
Stable temperatures due to large buffer tanks.
Optimum output conditions for pumps.
Flexible retrofitting of pumps and water technology.
SAND FILTER
Removal of solids is important for high
operational safety and proper water quality.
All larger particles (200 µm) in the main stream are removed with a sieve cloth to protect plant components.
Monitoring and a bypass circuit are important here. In a separate side stream, on the other hand, even the finest solids (5 µm) should be continuously removed, e.g. with a filter cartridge or a sand filter. Otherwise, this could lead to silting or deterioration of water additives. Depending on the design, automatic cleaning of the filter by backwashing is possible.
HEAT RECOVERY
The heat generated during the cooling process can be recovered and used for indoor heating. This is often used in conjunction with hydraulic cooling in plastics plants.
PIPING
Piping must be of sufficient dimensions to prevent losses.
Minimum pressure rating of 16 bars.
Optimum flexibility and clarity
Various materials for the respective application (CU, SS, PVC, PP, PE)
Optimum insulation to avoid temperature fluctuations
SOFTENING
If the make-up water contains too much lime, or lime deposits are to be expected due to the operating conditions (high temperatures, evaporation), softening of the make-up water is necessary. Occasionally, under particularly critical conditions, complete desalination of the make-up water is required.
To soften the make-up water, ion exchangers are used, which exchange the calcium and magnesium ions that form deposits for sodium ions. If the exchange capacity is exhausted, the ion exchanger is regenerated with a saline solution and becomes available again. The regeneration process is fully automatic.
With softened water, lime scale deposits can no longer occur. Softened water cannot build up natural corrosion protection due to its lack of hardness; depending on the material, the use of a corrosion protection agent is then required.
VSD-CONTROLLED COMPRESSORS
A chiller rarely runs permanently at 100% full load. The use of modern speed-controlled compressors, which are infinitely variable in their power range from 16% to 100%, allows them to be operated with significantly lower energy consumption, especially in partial load operation.
REFRIGERANTS
Phase down, the gradual reduction of HCFC-containing refrigerants, will have the greatest influence on refrigerant choice in the coming years. The trend is continuing towards natural refrigerants with very low GWP values. Here, other factors, such as flammable, toxic or explosive properties, must be taken into account in the design of a system.
The choice of refrigerant also has an influence on the energy efficiency of a system, making a decisive contribution to the nature of a cooling system.
PUMPS
The consumer pumps on our refrigeration systems are equipped with pressure-dependent, speed-controlled drives. This reduces the energy consumption of the pumps by up to 40%.
Pumps from the L&R ECOPRO efficiency range are also speed-controlled and, in the case of the KSB pump, are equipped with SuPremE drives. The combination of synchronous reluctance motors and frequency converters allows high energy savings, especially during partial load operation.
WINTER RELIEF
“Winter relief” can be used whenever the outside temperature is lower than the required process temperature. In this scenario, outside air is used for cooling. A free cooling unit used for this purpose can also be used in summer, e.g. in plastics plants, to provide additional cooling for the hydraulic circuit.
FILTER TECHNOLOGY
Stainless steel strainer basket filters with bypass for cleaning during operation.
Protects the system against impurities and blockages in the heat exchanger channels. Reduces deposits of biological matter.
Your contact partners for high-quality
Split chillers
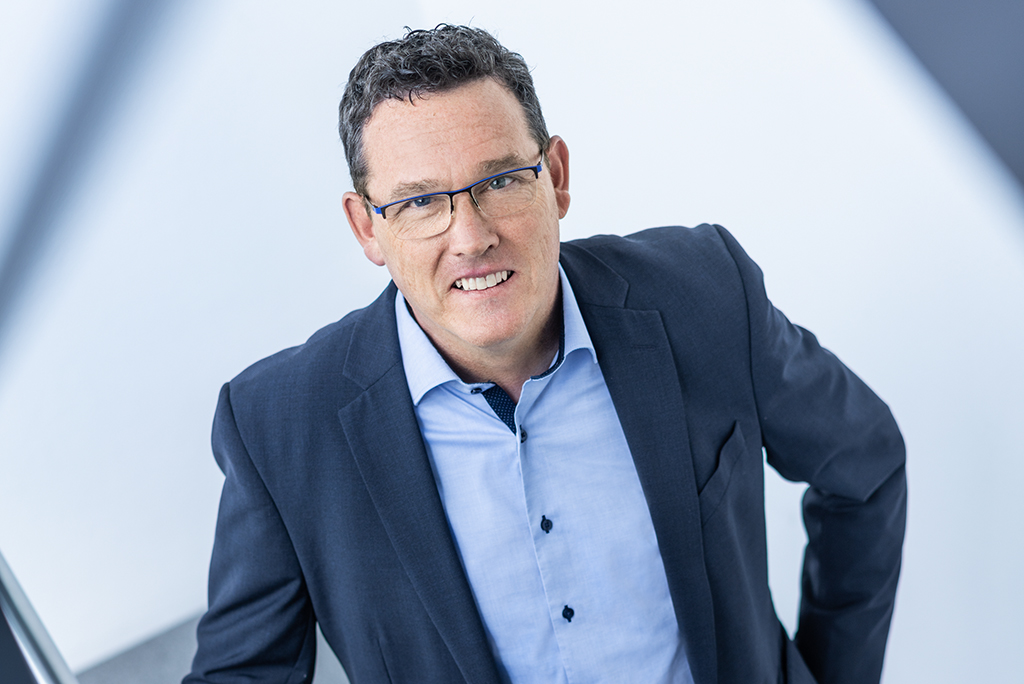
THOMAS IMENKÄMPER
Management (CSO)
Phone +49 2935 965-20
t.imenkaemper@lr-kaelte.de
Postcode areas (Germany) 01-04, 06-10, 12-19, 32, 33, 39-42, 44-49, 58, 59, 95, 96, 98-99
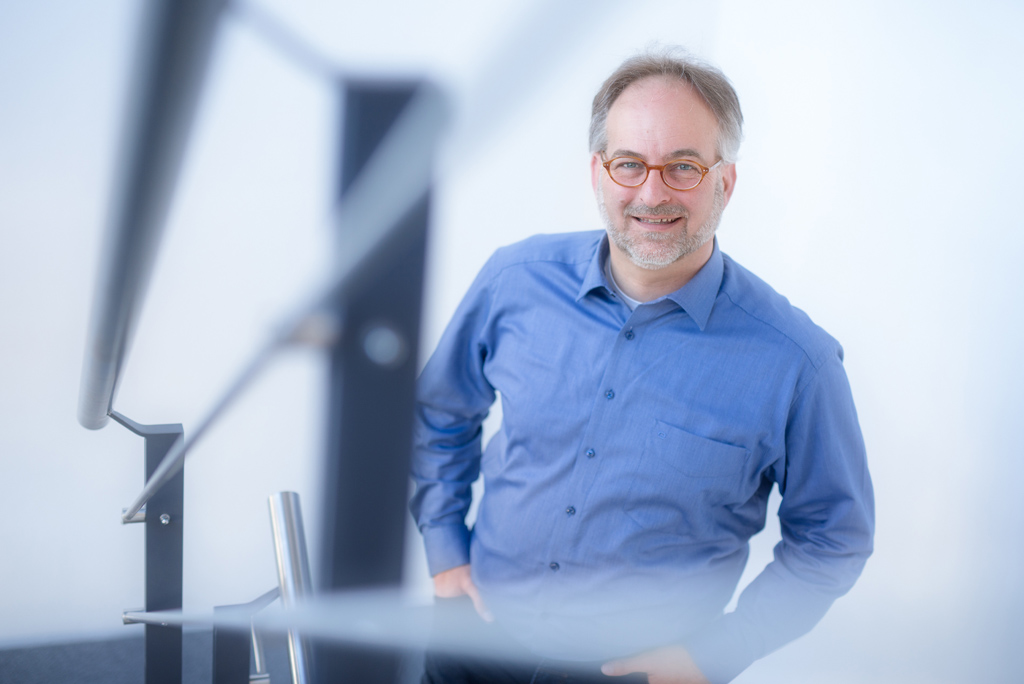
GEORG HESSE
SALES
Phone +49 2935 9652-203
g.hesse@lr-kaelte.de
Postcode areas (Germany) 34, 35, 50-56